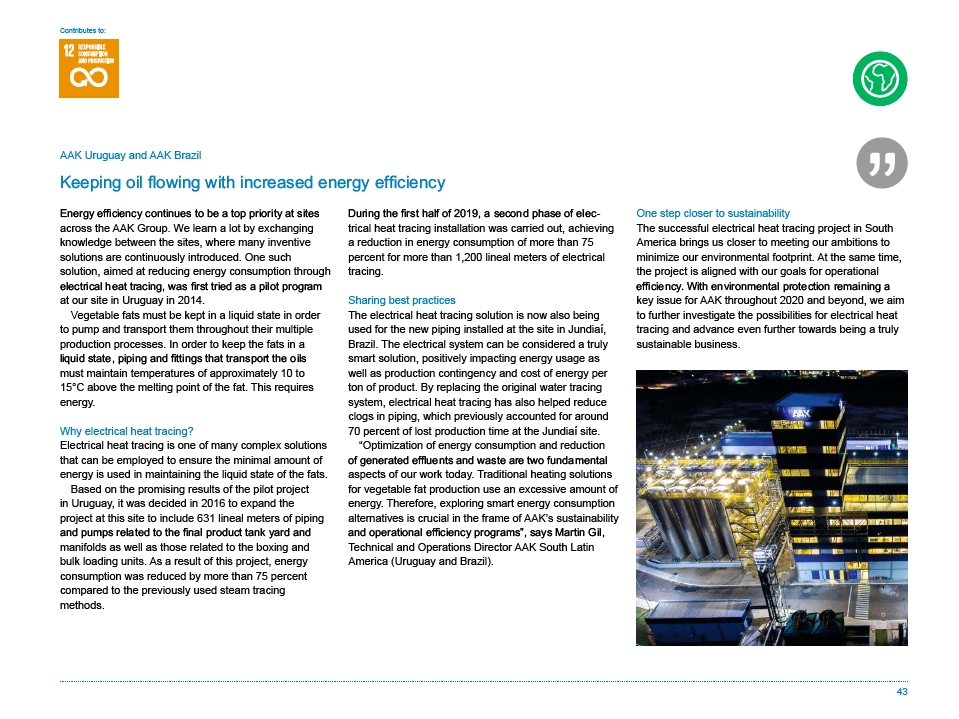
43
Contributes to:
AAK Uruguay and AAK Brazil
.HHSLQJRLOÀRZLQJZLWKLQFUHDVHGHQHUJ\HI¿FLHQF\
(QHUJ\HI¿FLHQF\FRQWLQXHVWREHDWRSSULRULW\DWVLWHV
across the AAK Group. We learn a lot by exchanging
knowledge between the sites, where many inventive
solutions are continuously introduced. One such
solution, aimed at reducing energy consumption through
HOHFWULFDOKHDWWUDFLQJZDV¿UVWWULHGDVDSLORWSURJUDP
at our site in Uruguay in 2014.
Vegetable fats must be kept in a liquid state in order
to pump and transport them throughout their multiple
production processes. In order to keep the fats in a
OLTXLGVWDWHSLSLQJDQG¿WWLQJVWKDWWUDQVSRUWWKHRLOV
must maintain temperatures of approximately 10 to
15°C above the melting point of the fat. This requires
energy.
Why electrical heat tracing?
Electrical heat tracing is one of many complex solutions
that can be employed to ensure the minimal amount of
energy is used in maintaining the liquid state of the fats.
Based on the promising results of the pilot project
in Uruguay, it was decided in 2016 to expand the
project at this site to include 631 lineal meters of piping
DQGSXPSVUHODWHGWRWKH¿QDOSURGXFWWDQN\DUGDQG
manifolds as well as those related to the boxing and
bulk loading units. As a result of this project, energy
consumption was reduced by more than 75 percent
compared to the previously used steam tracing
methods.
'XULQJWKH¿UVWKDOIRIDVHFRQGSKDVHRIHOHF-
trical heat tracing installation was carried out, achieving
a reduction in energy consumption of more than 75
percent for more than 1,200 lineal meters of electrical
tracing.
Sharing best practices
The electrical heat tracing solution is now also being
used for the new piping installed at the site in Jundiaí,
Brazil. The electrical system can be considered a truly
smart solution, positively impacting energy usage as
well as production contingency and cost of energy per
ton of product. By replacing the original water tracing
system, electrical heat tracing has also helped reduce
clogs in piping, which previously accounted for around
70 percent of lost production time at the Jundiaí site.
“Optimization of energy consumption and reduction
RIJHQHUDWHGHIÀXHQWVDQGZDVWHDUHWZRIXQGDPHQWDO
aspects of our work today. Traditional heating solutions
for vegetable fat production use an excessive amount of
energy. Therefore, exploring smart energy consumption
alternatives is crucial in the frame of AAK’s sustainability
DQGRSHUDWLRQDOHI¿FLHQF\SURJUDPV´VD\V0DUWLQ*LO
Technical and Operations Director AAK South Latin
America (Uruguay and Brazil).
One step closer to sustainability
The successful electrical heat tracing project in South
America brings us closer to meeting our ambitions to
minimize our environmental footprint. At the same time,
the project is aligned with our goals for operational
HI¿FLHQF\:LWKHQYLURQPHQWDOSURWHFWLRQUHPDLQLQJD
key issue for AAK throughout 2020 and beyond, we aim
to further investigate the possibilities for electrical heat
tracing and advance even further towards being a truly
sustainable business.